


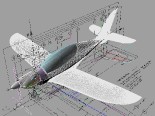


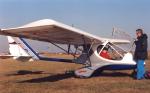
COMP-LET Shark |
![]() |
![]() |
Shark will be offered in two versions - European UL with retractable gear and simpler LSA with bigger wing and fixed landing gear. Although UL European requirements limits MTOW, both versions are calculated and will be tested for max take-off weight 600 kg. Advanced Aerodynamic DesignTo reach as small as possible aerodynamic drag Shark uses own airfoil, optimized for fast cross-country flights, prepared by aerodynamics from famous turboprop military trainer producer, trapeze wing with elliptical leading edge in its aileron part , smooth fuselage and fin shape, and undercarriage with main legs folding during its retracting – like in the jet-fighters. Comfortable roomy cockpit700+ mm wide cockpit with adjustable seats and EFIS/EMS instruments for both pilots are standard. All is optimized for the crew comfort during long cruise flights – with left hand on the fighter-like lever-throttle and side-stick in right hand. Quality and safetyTECHNOLOGY - Advanced composite structure uses carbon, aramid and glass fibres as weaved fabrics, biaxial fabrics, unidirectional tapes, sleeves and roving together with epoxy resin. PVC foam. and aramid honeycomb is used for sandwich panels. Different materials are used on structural components, where their properties gives the best ratio of weight and stability, stiffnes and passive safety. Carbon - today one of the best construction material - is often used on details, which are normally produced from steel or aluminium, as this saves kilograms. Parts are produced with handlamination process, but low temperature prepregs, infusion and RTM process, together with pultruded profiles and filament wound and sleeve tubes will be tested with developing process, to get the best results in quality, weight and technology. CNC foamcutting and milling is used for developing process as well for cutting and trimming composite parts in serial production. Aircraft is PRODUCED in modern facilities of the company COMP-LET Senica, Slovakia - www.complet.sk . COMP-LET is one from the biggest European producer of composite parts for light aeroplanes. Company have today 200 qualified employees, a lot of experience in composite mass production as a 16 year supplier of Diamond Aircraft - DA40, DA42, SuperDimona, Katana, Aerospool-Dynamic, Flysynthesis-Texan, Wallaby, Aeropro-Eurofox, FK-Leichtflugzeuge-Polaris. Production is EASA and national CAA approved. We believe ,that all can guarantee the biggest quality of final product for our customers. DesignShark project is built on the background of our good collaboration in MD3 Rider development and its logical continuing – to use COMP-LET long-time experiences with composites and Gryf design team experiences from various developments and designs of hang-gliders, commuters, gliders and GA to worldwide known ultralights – and try to create the best what we are able to. Designed according to Czech and Germany ultralight and US Light Sport Aircraft requirements.
Technical descriptionA monocoque composite FUSELAGE with integral fin is created from glass-epoxy skin, stabilized by PVC foam and honeycomb sandwich, with local reinforcing for all subassemblies fixing. Composite cockpit interior panels creates arm rests, seat backs, floors and instrument panels – and strength reinforcing itself. Under front pilot seat rest there is created wing spar box, enlarged into short independent center part of wing, in which both main spars are connected by quick-dismountable pins. Rear central wing part spar under rear seat carries rear wing beam hinges. On the sides of center part – between both spars, there are brackets and hinges of retractable landing gear. In the rear fuselage is supporting conventional tail surfaces hinges, glued into locally reinforced composite shell. Welded engine mounting, undercarriage and control system brackets and cockpit equipment are fixed into fuselage by bolts. Not divided single-piece CANOPY, open-able from the port-side is supported by gas braces and enables uncompromising visibility. Composite WINGS have carbon-fiber main spar, rear help-beam for flaps and aileron fixing and integral fuel tanks between wing beams. Ribs are in the place of fuel tanks, aileron and root only. Wings have own specially designed efficient 14% JS airfoils and classic ailerons. 60% span efficient double-slotted flaps with 15o, 30 o, and 45o deflection are hinged on the rear wing spar in three carbon hinges. The same technology composite horizontal TAIL with 13% symmetrical LS profile is connected on keelson hinges by 2 pins and 2 bolts. Push-rod controlled ELEVATOR has electrically controlled trim-tab. Rudder is controlled by control cables in leading plastic tubes. Wings and horizontal tail surfaces can be quickly dismounted for transportation or storage. Tricycle type landing gear, with steerable 13x4" nose wheel and 14x4” main wheels with hydraulic disc brakes, controlled by brake levers from both pilot places. LSA fixed undercarriage has composite main undercarriage legs and simplified front leg, welded from 4130. Standard UL version retractable undercarriage has retractable version of fixed front leg, and main landing legs units welded from 4130 tubes with classic shock absorbers , hinged out of axis, to enable main legs folding into minimal space. Full dual control with starboard sidesticks and pedals for both pilots.Flap lever and throttle are placed on the left panel, trim lever is controlled from side-sticks buttons. Elevator and Ailerons are controlled by rods, Rudder is controlled by cables in plastic glide tubes. Flaps are controlled by electric actuator placed in the cockpit floor (under rear seat). Instrument panel with standard EFIS/EMS instruments for both pilots are completed with classic fuel gauges, radio ICOM A200, transponder and GPS and doubled basic 60mm speedmeter and altimeter, full cockpit upholstery with adjustable seats. Design accessContinuing - Shark project is connecting producer experiences with composites and Gryf design team long time skills in aircraft development - from commuters like L-410 through General Aviation airplanes and gliders as L23 Blaník to ultralights Gryf, Skyboy, or MD3 Rider and a lot of other, flying in thousands worldwide - to offer the best combination between good quality and performances, simple structure, perfect aerodynamic shape and enough cabin comfort to enjoy longer trips. Gryf basic philosophyGood performances, comfort, peculiar styling, great life, acceptable cost - and exceptional aptitude for cross country. PerformancesTo reach as small as possible aerodynamic drag for fast cross-country flights, Shark’s aerodynamicists chosen semi-elliptic wing - a combination of trapeze wing in flap section with the rest of the wing with elliptical leading edge. In the same time Shark uses own airfoil prepared especially for that plane - with “bubble” on its polar diagram - in the place of faster cruise speeds. This local curved characteristic decrease aerodynamic drag coefficient under 0,004 – by still enough high lift coefficient. To help aerodynamic shape, main undercarriage is folded during its retracting, to need as small volume and wheel covers as possible. Shark interior
Interior styling is created by Peťo Zelman from Academy of Fine Arts and Design, Bratislava. Original interior uses left side lever throttle and choke and right-side sidesticks. Standard flight instruments includes EFIS/EMS displays for both pilots and GPS, with doubled analog speedmeters and altimeters. From first time of development we chosen Sharks interior as our “trade mark” = fighter-like, comfortable, ergonomic, safety.
Styling
Good styling of the machine means to create some mechanical creature – the fellow animal with own „face“. We prefer the pilot feels like a not-divided part of the aircraft being, when aircraft is controllable by Your mind – not to recognize, where Your body is ending and aircraft begins …
Tom Gunnarson, the president of Light Aircraft Manufacturers Association (LAMA) described his feelings from “Riding the LSA SportRider” in his Pilot Report, published in Ultralight Flying! magazine: “Looking like a shark fin, the raket-back vertical stabilizer protruding high above the tail section may have been included to set the design apart, or maybe the designer felt such a shape provided some benefit in performance or safety value …” -so we tried to cover his feelings. Started from that logo, we are continuing in whole Shark aircraft development... feeling is the main.
Shark at AERO Friedrichshafen 2009 |